Little bit Engineering of SDG"LEOS"
A Global Initiative:
Sustainable Development Goals (SDGs)
17 Goals to Change the World

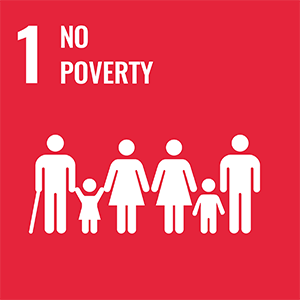
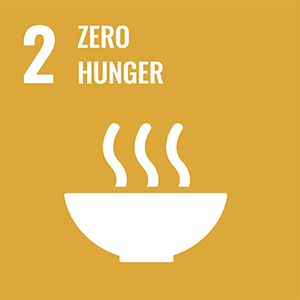
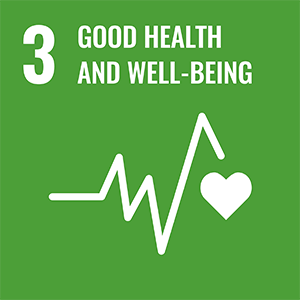
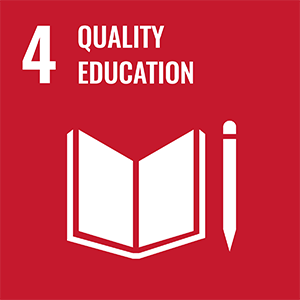
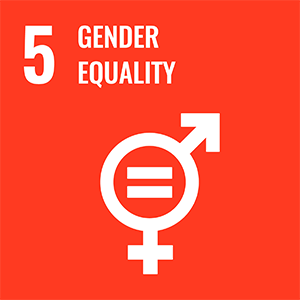
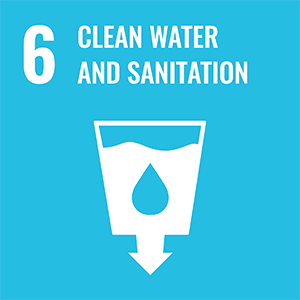
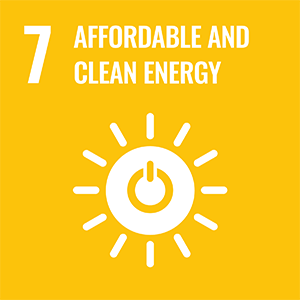
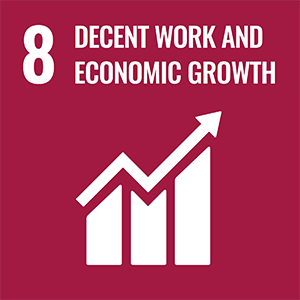
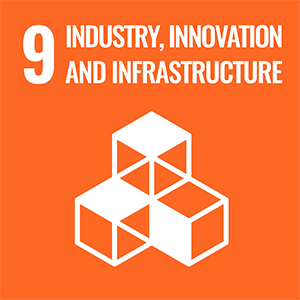
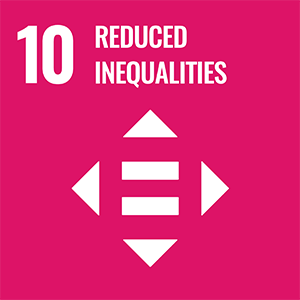
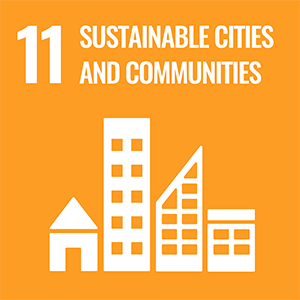
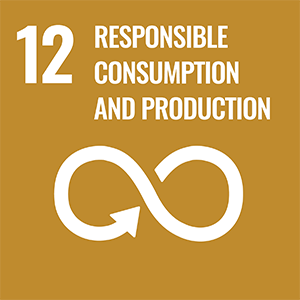
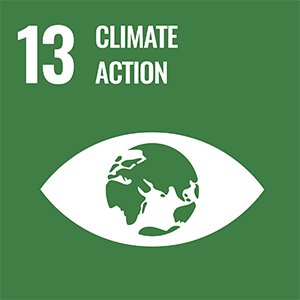
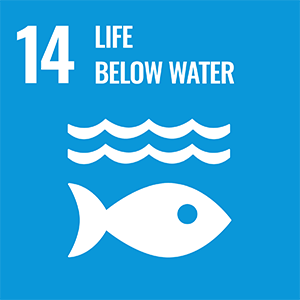
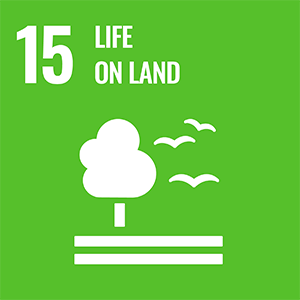
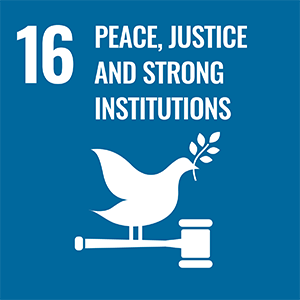
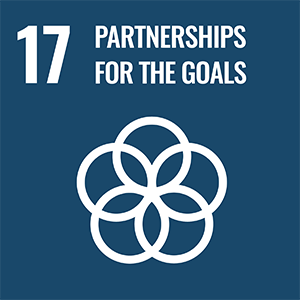
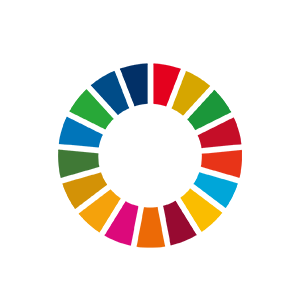
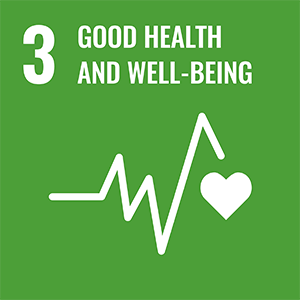
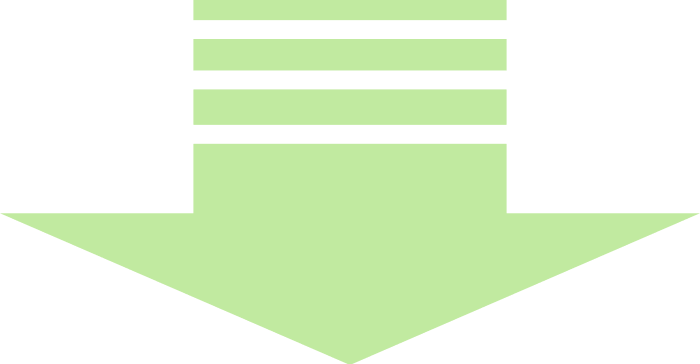
What is "LEOS"? (Little bit Engineering of SDG)
We work out solutions for your spot of trouble, by combining our products (such as blowers and Mistresa models) with the various pieces of surrounding equipment. "LEOS" represents what we do as a company. The people coming up with flexible solutions in response to the issues our customers face are our team of experts who hold licenses stipulated in ordinances such as the Prevention of Organic Solvent Poisoning, the Prevention of Hazards due to Specified Chemical Substances, and the Prevention of Hazards Due to Dust. In addition to suggesting solutions, we also respond rapidly to requests for repairs and maintenance of machines. Please don’t hesitate to consult us, no matter what your spot of trouble involves— we will use our engineering skills to create safe, comfortable work spaces.
We will propose the optimum environment improvement according to the use!

- SDG’s service
- Case Studies
SDG’s service
Work environment improvement “What SDG can do”
- Step.0Grasping of substances used
- Step.1Grasping of current situation
(working environment measurement) - Step.2Improvement equipment planning
(engineering and equipment measures) - Step.3Equipment construction
- Step.4Confirmation of effect
(working environment measurement) - Step.5Maintenance and confirmation of persistence
-
Step.0Grasping of substances usedBased on the safety data sheet (SDS), grasp the substances included in the chemical agents currently used by the business owner.
Check for the presence or absence of harmfulness.* The manufacturer is obliged to report the SDS to the sale destination. -
Step.1Grasping of current situation (working environment measurement)Measure the environmental concentration in the work process and check if the measured concentration is the acceptable concentration or less in the working environment.
LEARN MORE
Measurement of exposure of moving worker Evaluating Respirators with Fit Testing Fit Testing Service SDG conducts quantitative fit testing, an evaluation method that has been adopted worldwide.- What is fit testing?
-
Fit testing is used to determine the suitability of the welding respirators typically worn by workers.
This service uses a dedicated measuring device to determine whether a particular respirator fits a worker’s face perfectly.
On April 1, 2023, fit testing becomes a legally required procedure.
- SDG’s Services
-
-
We perform quantitative fit testing that meets global standards.
-
Since we report the testing results in numerical form, the purchaser can use the information provided to make the proper choice.
-
The results of the fit test can be used to identify needed improvements to the work environment.
-
-
- Fit Testing Methods
-
Two fit testing methods are available: the quantitative fit test and the qualitative fit test.
Measurement records must be retained for a period of three years. -
-
Quantitative Fit Test
-
- Results are recorded with a dedicated measuring device.
- Accurate numerical values can be obtained.
- Qualitative Fit Test
-
- The subject is asked to detect taste and odor during the test procedure.
-
Quantitative Fit Test
-
At SDG, we provide highly accurate quantitative fit tests designed to improve the work environment.
Measurement of respiratory protection (fit test) Existing equipment working environment measurementWork fixed point working environment measurementWorking environment measurement result report
(Certificate)After working environment measurement, 1st to 3rd management categories are applied. Onlya working environment measurement agency can make working environment measurements.
SDG is a working environment measurement agency registered company.
We can measure and evaluate the concentration!We will provide one-stop actions not only for examination, planning, designing, notification, construction, inspection/maintenance, environment measurement and production execution but also for notification document and working environment assessment.CLOSE
-
Step.2Improvement equipment planning (engineering and equipment measures)Based on the environment measurement result and the laws and regulations, make improvement equipment planning and submit a plan to the relevant public office as needed.
LEARN MORE
1. Engineering measures and preparation of notification document Based on the environment measurement result, plan equipment complying with the laws and regulations.Engineering measures: Designing and construction of exhaust system and dust collectorNotification document: Preparation of application form for Labour Standards BureauMeasures for fundamentally eliminating dangerous work are called qualitative measures (essential safing). When it is difficult to solve problems with qualitative measures, pursuant to engineering measures (equipment measures), measures using equipment and management measures are considered. Personal protective equipment is positioned as final measures.2. Visualization of existing duct Visualize the existing piping equipment and conduct properness diagnosis.3. Making an airflow analysis for avoiding a risk at the time of introduction of new equipment Airflow Analysis Service We solve problems such as excessive heat accumulation in order to optimize the temperature inside the plant.Before implementationAfter implementationWe provide manufacturer-support services by utilizing thermal fluid analysis software and employing the expertise we have acquired as a blower manufacturer to optimize factory temperatures.- POINT!
-
- Addressing excess heat
- Providing overall ventilation
- Increasing the efficiency of existing air conditioning equipment
- Analyzing the movement of suspended particles and developing countermeasures
Pre-installation simulations can eliminate the need for corrective work and other wasteful remedies.Video for confirmation of effect4. Digital Mapping Service We will examine and analyze your plant and suggest improvements to the work environment.-
1Customer’s plant
- Typical measurement challenges
-
- Plant is large.
- Structure is three-dimensional.
- Ductwork and piping are complex.
- Structure requires a long time to examine.
-
2Survey with 3D laser scanning tools
provides point cloud data of the plant. -
33D CAD data provided by SDG.
To provide technical services to our customers, our specialist employees obtain survey data with dedicated measuring instruments.- Details of SDG’s Digital Mapping Service
-
IllustrationScanned point cloud data is converted to 3D CAD data to facilitate planning of new ductwork and piping.3D-laser-scanned point cloud dataConversion to 3D CAD dataData recordingThe results of the survey and examination are incorporated into dedicated publications.Diagram of ductworkDesignBecause detailed site information is recorded, confirmation work can be performed with accuracy at the desk.AnalysisThe created 3D model can be used to perform airflow analysis that includes wind speed, static pressure, temperature, pollution levels, and noise levels.Targets for improvement of overall ventilation as well as countermeasures for excess heat are highlighted.Construction planA construction plan can be developed with reference to the actual onsite situation.Equipment maintenanceA maintenance list can be created by layering the target devices in the scanned data.
CLOSE
-
Step.3Equipment constructionInstallation of devices and related equipment
LEARN MORE
1. General ventilation and measures against heat Produce air flow wholly to prevent retention of hot air, gas, etc.2. Push-pull type ventilation system It produces very small air flow at a generation source to provide ventilation.PPV type downward flow systemPPH type horizontal flow systemAir blower for VentiresaVentilation to outside3. Sideward suction system It performs sucking from the side of a generation source.4. Downward suction system It performs sucking from the side of a generation source.5. Movable arm type suction system It performs sucking from above using the movable arm.CLOSE
-
Step.4Confirmation of effect (working environment measurement)
-
Step.5Maintenance and confirmation of persistenceConfirm the persistence of the effect of the constructed equipment and perform periodic maintenance of it.
- After confirming the working environment measurement (obligation), prepare a report (self-management).
- After confirming the periodic voluntary inspection (obligation), prepare a report (self-management).
LEARN MORE
Inspection, repair and cleaning We will perform cleaning and maintenance, including the piping after installation.
We will handle equipment whether it is new or existing equipment and whether it is our company’s or other companies’ equipment.Cleaning of duct piping Before implementationAfter implementationCleaning of impeller of air blower Before implementationAfter implementationAdjustment of balance of impeller Periodic inspection, diagnosis and repair Inspecting and surveying large areas and high structures from altitude SDGs & Drone Services We offer simple inspections of equipment at height and in plants.Our specialist employees provide technical services to customers by acquiring data with drones.- Typical Services
-
Dimensions can be confirmed with point cloud data, and information can be shared through the cloud once it has been processed into 3D data using a technology called Structure from Motion (SfM), a photogrammetric range imaging technique. This process combines multiple images captured at mapped inspection points.*No data will be disclosed to third parties.● 3D modeling ● Recording ● Construction planning● Orthomosaics● Equipment maintenance and inspection
- Periodic voluntary inspections of local exhaust equipment
-
- Inspecting for duct breakage, corrosion, and clogging
- Checking nameplates of air extractors installed at height
- POINT!
-
- Improved worker safety
- Inspection and surveying of large areas and high structures
- Reduced costs, minimized labor, and other advantages
Service Flow Diagnosis by the customer following examination of delivered dataCLOSE
Case Studies
-
Building Material Processing Industry
- Exhaust ventilation for organic solvent application work
- Local exhaust ventilation
-
LEARN MORE
-
Printing Industry
- Exhaust ventilation for the gravure printing process
- Local exhaust ventilation
-
LEARN MORE
-
Qualification training center
- Welding fume dust removing exhaust
- Local exhaust ventilation
-
LEARN MORE
-
Constuction Equipment Industry
- Welding Fume
- Local exhaust ventilation
-
LEARN MORE
-
Rubber processing Factory
- To exhaust organic solvents during rubber processing
- Local exhaust ventilation
-
LEARN MORE
-
Lens production
- Reconstruct local exhaust for organic solvent exhaust system
- Local exhaust ventilation
-
LEARN MORE
-
Exterior wall board manufacturing industry
- Exterior wall board coating
- Local exhaust ventilation
-
LEARN MORE
-
Automobile Parts Manufacture
- Exhaust for part paint correction
- Local exhaust ventilation
-
LEARN MORE
-
Paint manufacture
- Organic solvent exposure countermeasures
- Local exhaust ventilation
-
LEARN MORE
-
Food manufacturer
- Steam exhaust from sterilization furnaces
- Local exhaust ventilation
-
LEARN MORE
-
Building Equipment Manufacturing
- Local exhaust system for painting
- Local exhaust ventilation
-
LEARN MORE
-
Bearing Manufacturing
- Exhaust for bearing cleaning process
- Local exhaust ventilation
-
LEARN MORE
-
Parts manufacturing industry
- Local exhaust during painting process
- Local exhaust ventilation
-
LEARN MORE
-
Chemical Raw Materials Manufacture
- Measures to prevent exposure to specified chemical substances
- Push-pull
-
LEARN MORE
-
Material Testing Facility
- Ventilation system for organic solvent application work
- Push-pull
-
LEARN MORE
-
Manufacturing of functional materials
- Ventilation of materials containing organic solvents
- Push-pull
-
LEARN MORE
-
Manufacture of parts for industrial machinery and optical equipment
- Exhaust air during optical equipment cleaning process
- Push-pull
-
LEARN MORE
-
Manufacture for industrial air conditioners
- Optimized air volume and improved work efficiency by adopting push-pull
- Push-pull
-
LEARN MORE
-
Manufacture of water pipes
- Push-pull ventilation system for painting pipes in various lengths
- Push-pull
-
LEARN MORE
-
Various
- Local exhaust organic solvent for touch up procedure
- Push-pull
-
LEARN MORE
-
Signboard Manufacturing
- Installation of local exhaust ventilation in the bonding process
- Push-pull
-
LEARN MORE
-
Manufacture of functional materials
- Coating process push-pull ventilation
- Push-pull
-
LEARN MORE
-
Spice manufacturing
- Ventilation of gas containing organic solvents dispersed during weighing
- Push-pull
-
LEARN MORE
-
Metal processing
- Odor ventilation and exhaust heat from the adhesive application
- Push-pull
-
LEARN MORE
-
Automobile Parts Manufacture
- Preventing scattering of dust generated at the parts loading opening
- Dust collection
-
LEARN MORE
-
Metal Parts Manufacturing Industry
- Dust collection for polishing work emitting sparks
- Dust collection
-
LEARN MORE
-
Industrial Rubber Products Manufacturing Industry
- Collection of dust generated by the rubber kneading machine
- Dust collection
-
LEARN MORE
-
Synthetic Material Processing Industry
- Dust collection during Bakelite processing
- Dust collection
-
LEARN MORE
-
Industrial material manufacturing industry
- Dust control in the stiring of industrial materials
- Dust collection
-
LEARN MORE
-
Livestock feed manufacturing
- Emissions when weighing raw materials for livestock feed
- Dust collection
-
LEARN MORE
-
Piping Materials Manufacturing Industry
- Dust collection of NC router resin processing powder
- Dust collection
-
LEARN MORE
-
Train Garage
- Localized dust collection during filter cleaning process
- Dust collection
-
LEARN MORE
-
Casting Manufacturing
- Dust collection for dismantling casting molds
- Dust collection
-
LEARN MORE
-
Fluoropolymer Fluid Equipment Manufacture
- Dust control in raw material preparation process
- Dust collection
-
LEARN MORE
-
Machinery manufacturer
- Melting Furnace High-Temperature Dust Collector
- Dust collection
-
LEARN MORE
-
Exterior wall manufacturing industry
- Collection of dust and iron scraps
- Dust collection
-
LEARN MORE
-
Glass fiber production
- Dust collection during the weighing of raw materials
- Dust collection
-
LEARN MORE
-
Automobile Parts Manufacture
- Collection of mist generated during testing
- Mist collection
-
LEARN MORE
-
Automobile Parts Manufacture
- Collection of large volumes of soot generated during testing
- Mist collection
-
LEARN MORE
-
Cutlery Manufacturing Industry
- Collection of soot generated during cutlery processing
- Mist collection
-
LEARN MORE
-
Metal Parts Manufacturing Industry
- Mist collection for polishing work
- Mist collection
-
LEARN MORE
-
Machining parts for machine tools
- Measures against oil mist in open machine tools
- Mist collection
-
LEARN MORE
-
Automobile Parts Manufacture
- Collecting mist from a processing machine that generates a large quantity oil droplets
- Mist collection
-
LEARN MORE
-
Cutting Tool Manufacturing Industry
- Oil mist collection with timer function
- Mist collection
-
LEARN MORE
-
Pipe Manufacturing
- Oil mist collection and cutting oil blowing on pipe cutting machine
- Mist collection
-
LEARN MORE
-
Metal press work
- Installation for preventing mist dispersion
- Mist collection
-
LEARN MORE
-
Construction equipment manufacturing
- Mist collection from centerless grinding machine without cover
- Mist collection
-
LEARN MORE
-
Metal Parts Manufacturing Industry
- Cleaning of the blower impeller
- Maintenance
-
LEARN MORE
-
Metal Parts Manufacturing Industry
- Collection of dust generated by the Burring machine
- Maintenance
-
LEARN MORE
-
Heavy duty vehicles repairs industry
- Other companies' blower maintenance
- Maintenance
-
LEARN MORE
-
Parts manufacturing
- Maintenance of V-belt driven blowers & Seminar
- Maintenance
-
LEARN MORE
-
Automobile Parts Manufacture
- Modification of the duct inspection opening
- Other
-
LEARN MORE
-
Sugar manufacture
- Insect control measures in the shipping process using conveyors
- Other
-
LEARN MORE
-
Medical instrument precision processing industry
- Improvement of air conditioning in the factory
- Other
-
LEARN MORE
-
Resin parts manufacturing plant
- Circulates air-conditioned cool air in the factory
- Other
-
LEARN MORE
-
Chemicals manufacturing plant
- Blowing off rubbish from mold release agents booth
- Other
-
LEARN MORE
-
Auto parts manufacturing
- Improved ceiling area temperatures
- Other
-
LEARN MORE
-
Event venue rental
- Mist generation in multi-purpose warehouses used for various events and other purposes to prevent heat build-up.
- Other
-
LEARN MORE
-
Parts painting
- Replace from V-belt driven blower to direct-drive blower.
- Other
-
LEARN MORE
-
Automotive parts manufacturing
- Reducing the number of fans on the production line
- Other
-
LEARN MORE
Building Material Processing Industry
- Exhaust ventilation for organic solvent application work
- Local exhaust ventilation
- Why we were consulted
- The company carried out working environment measurement at the direction of the Labor Standards Inspection Office, but the results were unacceptable, and the company was at a loss for what to do.
- Before
- After
- Equipment installed
-
- Enclosing hood
- Explosion-proof exhaust blowers
- K1S5E-1
- Installation work including ducts
- Improvements
- The working environment measurement results were raised to control category 1 (optimum category) and were deemed satisfactory by the Labor Standards Inspection Office.
Printing Industry
- Exhaust ventilation for the gravure printing process
- Local exhaust ventilation
- Why we were consulted
- The printing company had installed a downdraft extraction local exhaust ventilation system to fix an issue identified by the Labor Standards Inspection Office, but working environment measurements remained poor, and we proposed considering an enclosing hood.
- Before
- After
- Equipment installed
-
- Enclosing hood
- Explosion-proof exhaust blowers
- K1S5E-1
- Installation work including ducts
- Improvements
- The working environment measurement results were raised to control category 1 (optimum category) and were deemed satisfactory by the Labor Standards Inspection Office.
Qualification training center
- Welding fume dust removing exhaust
- Local exhaust ventilation
- Why we were consulted
- Because it was troublesome to maintain the filter of the dust collector for fumes generated in welding operation and using an air blower to exhaust air would scatter dust to the outside, they were in trouble regarding how to adopt a dust collector exhaust method.
- Before
- After
- Equipment installed
-
- KSB-H15B
- Cyclone
- Improvements
- By combining an air blower for fume exhaust and a cyclone, it became possible to prevent dust from scattering to welding fumes and the outside.
Constuction Equipment Industry
- Welding Fume
- Local exhaust ventilation
- Why we were consulted
- Welding work was performed during the maintenance of the construction equipment rental products, and welding fumes were generated. Due to the large working area, they need a movable fume collector.
- Before
- After
- Equipment installed
-
- CDF1
- Inverter
- Cable (1 set)
- Improvements
- The movable fume collector implemented has made it easy to move around and collect the fume in a large work area.
Rubber processing Factory
- To exhaust organic solvents during rubber processing
- Local exhaust ventilation
- Why we were consulted
- The processing area is next to the private house, so the customer was worried about the exhaust of odors, including the organic solvents generated during the processing. Besides, the air/fumes did not exhaust properly because the processing work position often changed.
- Before
- After
- Equipment installed
-
- MDF-KSB-2200-M211
- Improvements
- The blower for exhausting organic solvents was installed on the wall to save space, and the ducts were installed on the ceiling to exhaust air from the other side of the building. In addition, to exhaust the organic solvents generated from the work on the floor successfully, a moveable hood was installed.
Lens production
- Reconstruct local exhaust for organic solvent exhaust system
- Local exhaust ventilation
- Why we were consulted
- During the manufacturing process, a product containing an organic solvent gave off an odour, the original ventilation equipment could not kept up with the organic solvents concentration and did not fit within the standard, which was a problem.
- Before
- After
- Equipment installed
-
- AH-H07HT-L313
- Work environment measurement
- Documents preparation to be submitted to the labor board
- Improvements
- Expand the workspace by remodeling the local exhaust system and shorten the time required because of one-stop environmental measurement and submission of documents to the labor standards.
Exterior wall board manufacturing industry
- Exterior wall board coating
- Local exhaust ventilation
- Why we were consulted
- Since the dimensions and sizes of the objects to be painted are inconsistent, there were cases where the currently used exhaust system could not be applied. In addition, The customer have trouble because the smell of thinner was leaking.
- Before
- After
- Equipment installed
-
- AH-H22HT-H213
- Improvements
- To be able to handle items of various sizes to be painted, we have installed an exhaust system that uses a movable extendable hood. Also, when the equipment is idle, it can be retracted and stored.
Automobile Parts Manufacture
- Exhaust for part paint correction
- Local exhaust ventilation
- Why we were consulted
- There was a thinner's smell when working on the parts paint correction, and no window nearby. Also, no exhaust system nearby, so workers were bothered.
- Before
- After
- Equipment installed
-
- MDF-AH-1200HT
- Exhaust hood
- Improvements
- An explosion-proof blower and an exhaust hood were installed to exhaust the odour from the part correction paint work effectively.
Paint manufacture
- Organic solvent exposure countermeasures
- Local exhaust ventilation
- Why we were consulted
- Had a problem when putting paint in a container and mixing it when researching paint process, generated the smell of the paint containing organic solvents and the lack of ventilation in the workshop.
- Before
- After
- Equipment installed
-
- MD-AH-H37-H213
- Enclosed hood
- Exterior hood
- Improvements
- By attaching hoods to the paint mixing machine and paint container washing area and exhausting with an explosion-proof blower, we can prevent exposure to organic solvents.
Food manufacturer
- Steam exhaust from sterilization furnaces
- Local exhaust ventilation
- Why we were consulted
- The steam generated during the food container sterilization process was discharged to the outside using ducting, but the air volume was insufficient and could not exhaust properly.
- Before
- After
- Equipment installed
-
- AH-H22GHT-H113
- Improvements
- We solved the steam leakage around the sterilization furnace problem by utilizing the existing duct and adding a stainless steel blower.
Building Equipment Manufacturing
- Local exhaust system for painting
- Local exhaust ventilation
- Why we were consulted
- The Labor Standards Inspection Office had pointed out that the existing paint booth was not in compliance with the Ordinance on Prevention of Organic Solvent Poisoning.
- Before
- After
- Equipment installed
-
- T1S4GH-1M211
- T2S4FH-3M211
- Ducts, arm ducts, construction.
- Improvements
- The existing paint booth and new paint booth with movable arm type was installed local exhaust ventilation. Paint scattering decreased. Furthermore, the new installation was made in compliance with the organic regulations and succesfully reported to the Labor Standards Inspection Office.
Bearing Manufacturing
- Exhaust for bearing cleaning process
- Local exhaust ventilation
- Why we were consulted
- In the process of cleaning bearings that use organic solvents, solvent gas disperses in and out of the washing machine, causing environmental problems.
- Before
- After
- Equipment installed
-
- AH-H37-L213
- Hood fabrication
- Piping installation
- Local exhaust device notification documentation
- Improvements
- Gas dispersal during cleaning was prevented and effective exhaust ventilation was achieved. The vinyl curtains could be adjusted in the range of opening according to the work, and work efficiency was not affected.
Parts manufacturing industry
- Local exhaust during painting process
- Local exhaust ventilation
- Why we were consulted
- The increase in production led to more painting processes, but there was a shortage of paint booths.
- Before
- After
- Equipment installed
-
- MDF-AH-800 x 3 units
- Hood
- Compressor
- Installation and electrical work
- Notification Documents
- Improvements
- SDG suggested a local exhaust method for the paint booth and created a blueprint with a 3D model in advance, making the image of the local exhaust system easy to understand. Also, the fact that we handled all the installation and electrical work for the blower and equipment saved time by eliminating the need to contact multiple companies.
Chemical Raw Materials Manufacture
- Measures to prevent exposure to specified chemical substances
- Push-pull
- Why we were consulted
- Because the scope of work on chemical substance introduction processes is broad, the manufacturer was troubled by uncertainty over what kind of exhaust ventilation equipment would be best.
- Before
- After
- Equipment installed
-
- Push-pull hood PPHW-0909
- Explosion-proof intake/exhaust blowers MDF-AH-600
- Installation work including ducts/electrical work
- Improvements
- Introducing a push-pull type ventilation system enabled us to implement measures to protect workers from exposure and contain chemical generation sources.
Material Testing Facility
- Ventilation system for organic solvent application work
- Push-pull
- Why we were consulted
- Introducing a high velocity local exhaust ventilation system would have been impractical since precise measurement is necessary, so we proposed a push-pull ventilation system with slow wind velocity.
- Before
- After
- Equipment installed
-
- Push-pull hood PPH-0707
- Explosion-proof exhaust blowers MDF-AH-800
- Control panel CPW-07
- Installation work including ducts/electrical work
- Improvements
- Introducing a push-pull type ventilation system enabled us to expel organic solvents outdoors in a manner that did not impact precise measurement work.
Manufacturing of functional materials
- Ventilation of materials containing organic solvents
- Push-pull
- Why we were consulted
- When weighed materials containing organic solvents, there were multiple reports of headaches from workers due to the smell of organic solvents from the materials.
- Before
- After
- Equipment installed
-
- PPHWF-0906-A02
- MDF-AH-600
- Duct installation
- Electrical installation
- Document
- Improvements
- No longer senses the smell of materials containing organic solvents during weighing operations. We supported duct installation, electrical installation and documents.
Manufacture of parts for industrial machinery and optical equipment
- Exhaust air during optical equipment cleaning process
- Push-pull
- Why we were consulted
- The customer cleaned the optical equipment parts properly and made a handmade exhaust system with stretch film, pipe and hose but it did not exhaust well. The working environment was classified as category 2 by the Labour Standards Inspection Office every six months therefore they need to make improvement
- Before
- After
- Equipment installed
-
- PPHF-1507
- AH-H22
- Improvements
- The push-pull exhaust ventilator was adopted to improve the exhaust system. When they re-evaluated the working environment , it was classified as category 1, which means the work environment was improved.
Manufacture for industrial air conditioners
- Optimized air volume and improved work efficiency by adopting push-pull
- Push-pull
- Why we were consulted
- Adhesives containing organic solvents were used during the process of attaching insulation to equipment, an exhaust system was installed in each work space and exhausted with a large blower.
- Before
- After
- Equipment installed
-
- PPHW-0606
- K1S5E-2M212
- Improvements
- The use of a push-pull exhaust system improved ventilation and workability. In addition, the exhaust air volume has been optimized and airflow has been significantly reduced, this helps the customer saving on electricity costs.
Manufacture of water pipes
- Push-pull ventilation system for painting pipes in various lengths
- Push-pull
- Why we were consulted
- The customer is painting water pipes inside the factory, but due to multiple sizes of pipes, it is difficult to work, especially within the 6m range. Ventilation could not be done properly in a large area, and based on the results of environmental measurements, it was determined that need to improve the work environment.
- Before
- After
- Equipment installed
-
- PPHWF-1515
- MDF-AH-H37HT
- Ducting construction + wind speed measurement
- Improvements
- We installed a push-pull ventilation system with casters, making it possible to safely paint water pipes in large and small parts. Furthermore, using an MDF-type blower and adjusting the wind speed with an inverter can save energy when painting short pipes.
Various
- Local exhaust organic solvent for touch up procedure
- Push-pull
- Why we were consulted
- Organic solvents are generated during the touch-up process of painted products. In consideration of the health of workers, the generated organic solvents must be removed through ventilation.
- Before
- After
- Equipment installed
-
- PPHWF-0808
- MDF-AH-800
- Installation work + electrical work
- Report documents
- Improvements
- The push-pull device 'Ventiresa' attached to the lifting workbench allows multiple people to work on small parts and also enables touch-up painting of large parts by adjusting the height of the lifting workbench. Furthermore, it has become possible to exhaust organic solvents generated during work.
Signboard Manufacturing
- Installation of local exhaust ventilation in the bonding process
- Push-pull
- Why we were consulted
- Signboard fabrication plants use adhesives for bonding logos and letters, and the organic solvents generated during this process need to be exhausted. However, since signboards come in a variety of sizes and shapes, the problem was how to exhaust them.
- Before
- After
- Equipment installed
-
- Ventiresa
- MDF-AH-1000
- Installation work + electrical work
- Notification documents
- Improvements
- A push-pull device that can exhaust a large ventilation area improves the workplace environment, making work safer.
Manufacture of functional materials
- Coating process push-pull ventilation
- Push-pull
- Why we were consulted
- In the test process, methyl ethyl ketone was applied to the material in two separate locations. Therefore, there were two sources of organic solvents and the work area was filled with organic solvents.
- Before
- After
- Equipment installed
-
- AH-H10-A0Y×1 unit
- PPHWF-0707-A32×1 set
- Notification documents
- Installation and duct work (some existing equipment used)
- Electrical work
- Improvements
- SDG suggested moving the methyl ethyl ketone coating workbench from two separate locations to a single location and installing a push-pull ventilation system to allow simultaneous ventilation of the two workstations.
Spice manufacturing
- Ventilation of gas containing organic solvents dispersed during weighing
- Push-pull
- Why we were consulted
- Ventilation was required for gases dispersed during the weighing process of materials containing organic solvents. Since the work area was an explosion-proof zone, the equipment needed to be explosion-proof.
- Before
- After
- Equipment installed
-
- Push-pull ventilation system PPHW-0707 (special model)
- Blower MDF-AH-H15 for the push and pull sides x 2 units
- Improvements
- A push-pull ventilation system was installed in the workplace, A push-pull ventilation system was installed in the work area, and the use of filter boxes and explosion-proof blowers created a safe and comfortable work environment.
Metal processing
- Odor ventilation and exhaust heat from the adhesive application
- Push-pull
- Why we were consulted
- There was a need for simultaneous ventilation of the odor from the glue application process and the heat exhaust from the adjacent dryer.
- Before
- After
- Equipment installed
-
- MDF-AH-H15 (Explosion-proof)
- Push-pull type ventilation system (Ventiresa)
- Improvements
- By installing a push-pull ventilation system and connecting the dryer's heat exhaust hood to a flexible duct, it was possible to simultaneously vent the odor from the glue application process and the heat exhaust from the dryer.
Automobile Parts Manufacture
- Preventing scattering of dust generated at the parts loading opening
- Dust collection
- Why we were consulted
- The issue was situated at the parts loading opening on the conveyor belt. Any dust on the parts on the conveyor belt would fly into the air when they moved.
- Before
- After
- Equipment installed
-
- CFA-H515
- Hood with openable cover
- Improvements
- Closing the cover once the parts are loaded and using a dust collector to suction away the dust enabled us to prevent it from flying up into the air.
Metal Parts Manufacturing Industry
- Dust collection for polishing work emitting sparks
- Dust collection
- Why we were consulted
- In addition to scattering dust and sparks to surrounding areas during metal polishing and cutting, there was also a risk of fire.
- Before
- After
- Equipment installed
-
- GRM-H04T
- Sedimentation box
- Improvements
- Using a dust collector with a turbo blower to perform high pressure suction, and a sedimentation box to decrease fire causes, we were able to eliminate dust scattering and remove fire factors.
Industrial Rubber Products Manufacturing Industry
- Collection of dust generated by the rubber kneading machine
- Dust collection
- Why we were consulted
- Dust is generated by the raw rubber kneading machine during the kneading process. Because visual inspection was necessary during the process, an enclosing hood was impractical.
- Before
- After
- Equipment installed
-
- CFM-H40
- Enclosing hood (with transparent sheet)
- Improvements
- Parts that require visual inspection can be viewed through the transparent sheet hood. This also enabled prevention of dust scattering.
Synthetic Material Processing Industry
- Dust collection during Bakelite processing
- Dust collection
- Why we were consulted
- Bakelite is made of a wide range of compressed raw materials and large amounts of dust are scattered during the drying process.
- Before
- After
- Equipment installed
-
- CFA-H240
- Openable acrylic hood
- Improvements
- The acrylic hood enables work on processes that require visual inspection while also preventing scattering of dust.
Industrial material manufacturing industry
- Dust control in the stiring of industrial materials
- Dust collection
- Why we were consulted
- Dust generated in the process of weighing, feeding into and discharging from the equipment during the stirring operation was a problem for the workers.
- Before
- After
- Equipment installed
-
- CFM-H30
- Construction work
- Construction components (e.g. ducts)
- Improvements
- Local exhaust ventilation is installed in various locations to prevent dust from reaching the workers, and dust is collected by dust collectors. In addition, we also provide a one-stop service from the product to the construction service, so the construction period was shortened.
Livestock feed manufacturing
- Emissions when weighing raw materials for livestock feed
- Dust collection
- Why we were consulted
- The dust generated during the weighing of raw materials for livestock feed was troubling.
- Before
- After
- Equipment installed
-
- Enclosed hood (worktable) x2
- CFK-40 (explosion-proof) x2
- Improvements
- Custom made products were proposed to suit the production environment, and the work environment has become cleaner with after the installation of the explosion-proof dust collectors with the enclosed hooded worktables.
Piping Materials Manufacturing Industry
- Dust collection of NC router resin processing powder
- Dust collection
- Why we were consulted
- Resin powder was generated from the NC router resin processing machine, and the factory was covered with dust, making cleaning difficult.
- Before
- After
- Equipment installed
-
- CF-PC75033P1
- CF-2200H Dust explosion-proof model
- Guidance on installation at the time of delivery
- Improvements
- By connecting the duct directly to the cover of the router spindle section, the dust was efficiently collected with SDG's large pulse jet series dust collector.
Train Garage
- Localized dust collection during filter cleaning process
- Dust collection
- Why we were consulted
- There are large amount of dust generated when cleaning the used trains filters.
- Before
- After
- Equipment installed
-
- CFA-H515
- Workbench with hood
- Installation
- Electrical work
- Improvements
- By installing the workbench with hood and CFA-H515, the generated dust was successfully exhausted and cleaned smoothly. In addition, the installation and electrical work were done together, which shortened the installation period.
Casting Manufacturing
- Dust collection for dismantling casting molds
- Dust collection
- Why we were consulted
- When removing sand castings from molds, dust from the sand is scattered around, creating a poor working environment.
- Before
- After
- Equipment installed
-
- CFA-H410
- Duct work
- Improvements
- Working inside the enclosed hood prevents dust from scattering around.
Fluoropolymer Fluid Equipment Manufacture
- Dust control in raw material preparation process
- Dust collection
- Why we were consulted
- In the manufacturing process of fluoropolymer fluid equipment, mixing raw materials with lead monoxide (PbO) caused dust to dispersed from the workbench.
- Before
- After
- Equipment installed
-
- CF-3700H x 1 unit
- Draft chamber
- Notification Documents
- Installation work
- Duct work
- Electrical work
- Improvements
- A new draft chamber and a CF-3700H dust collector installed on the outdoor prevented dust from flying off the material.
Machinery manufacturer
- Melting Furnace High-Temperature Dust Collector
- Dust collection
- Why we were consulted
- Dust was scattered inside the factory when welding slag was collected from the gasification melting furnace, but installing a dust collector was difficult due to the high temperature.
- Before
- After
- Equipment installed
-
- CF-3700H extra-high-temperature furnace
- Improvements
- The suction piping was divided into two sections, and room-temperature air was sucked in from one section to lower the temperature of the gas entering the dust collector. This made it possible to suction and collect high-temperature dust.
Exterior wall manufacturing industry
- Collection of dust and iron scraps
- Dust collection
- Why we were consulted
- Dust was generated during the cutting of building material boards. Although a cyclone was installed, the increased cutting volume led to insufficient capacity of the existing cyclone.
- Before
- After
- Equipment installed
-
- CFB40-6FK
- Cyclone (40m3/min)
- Improvements
- By replacing it with an appropriate cyclone, dust from the cutting process was effectively collected, and the processing efficiency was improved.
Glass fiber production
- Dust collection during the weighing of raw materials
- Dust collection
- Why we were consulted
- To perform weighing, materials are transferred from the tank to a flexible container bag. A large amount of dust disperses from the inlet, but there was no space to install a hood.
- Before
- After
- Equipment installed
-
- CFM-H40 x 2 units
- Teflon laminated filter
- Installation work
- Duct work
- Improvements
- A ring-shaped hood covering the area around the inlet allowed dust to be collected without scattering.
Automobile Parts Manufacture
- Collection of mist generated during testing
- Mist collection
- Why we were consulted
- Mist is emitted from the drive unit during test driving. The configuration was another reason— enclosure under a hood was impractical as parts size varies greatly, meaning that there is also a large variation in the measurement device attachment position.
- Equipment installed
-
- CRH-15E
- Movable hood
- Improvements
- We secured a large work space for installing the test machine and enabled mist collection during testing without sacrificing workability.
Automobile Parts Manufacture
- Collection of large volumes of soot generated during testing
- Mist collection
- Why we were consulted
- Large volumes of soot are generated, and the manufacture wanted the simple maintenance option of filter replacement as the electric-type mist collector requires cleaning.
- Equipment installed
-
- Z-168 Special Mistresa (with differential pressure gage)
- Improvements
- This mist collector enables the simple maintenance option of filter replacement, and the differential pressure gage makes replacement timing clear.
Cutlery Manufacturing Industry
- Collection of soot generated during cutlery processing
- Mist collection
- Why we were consulted
- A mist- and soot-mix is generated. The Mistresa was discharging to a centralized duct, but soot was flowing into the duct and causing an oil leak.
- Before
- After
- Equipment installed
-
- CRM-H07-S23
- High-performance after-filter connectable to the duct
- Improvements
- We were able to reduce the amount of soot flowing into the duct and eliminate duct oil leaks.
Metal Parts Manufacturing Industry
- Mist collection for polishing work
- Mist collection
- Why we were consulted
- The mist generated in the polishing process was troubling, but equipment such as a crane was needed to place the materials in the polishing machine. This made it impractical to install a hood that enclosed the mist source.
- Before
- After
- Equipment installed
-
- CRM-H15-S23
- Movable hood
- Improvements
- We secured a large work space for placing the materials and prevented mist generated in the polishing process from being scattered to surrounding areas.
Machining parts for machine tools
- Measures against oil mist in open machine tools
- Mist collection
- Why we were consulted
- During the machining process on an open vertical lathe, could not installed the hood due to work reasons, and oil mist leaked from the ceiling.
- Before
- After
- Equipment installed
-
- Push-pull type Mistresa
- Improvements
- Installing the push-pull type Mistresa takes less space and reduced cost than installing a full cover. Also, the factory environment improved without changing workability.
Automobile Parts Manufacture
- Collecting mist from a processing machine that generates a large quantity oil droplets
- Mist collection
- Why we were consulted
- When processing parts, generating a large quantity of oil droplets and oil mist was leaking from the machine tool. The mist attached to the floor made it slippery and the machine got oily, which was a problem.
- Before
- After
- Equipment installed
-
- CRM-H07-S22 6 units
- Suction port with shield plate 6 pieces
- Improvements
- Installing a Mistresa and a suction port with a shield plate on the machining tool eliminates the problem of oil mist leakage, and the factory environment has become cleaner.
Cutting Tool Manufacturing Industry
- Oil mist collection with timer function
- Mist collection
- Why we were consulted
- The company manufactures high value-added products, which require long processing times (20 hours/unit). Therefore the customer would like to turn off the mist collector after the night operation by the timer control even when the employees are not present.
- Before
- After
- Equipment installed
-
- CRM-H02-S22
- Timer control panel (0.3 seconds to 30 hours)
- Installation + electrical work
- Improvements
- The working environment has become cleaner by having Mistresa and the timer control panel installed. The Mistresa power supply was also automatically shut off by the timer, so the company did not waste money on unnecessary electricity bills.
Pipe Manufacturing
- Oil mist collection and cutting oil blowing on pipe cutting machine
- Mist collection
- Why we were consulted
- The pipe cutting machine cut the pipe based on the size customer required. After the pipe cutting machine cut the pipe, the pipe was covered with oil stains, which took a lot time to clean up.
- Before
- After
- Equipment installed
-
- CRM-H04-S23
- Construction
- Improvements
- SDG suggested customer to install a mist collector MISTRESA on the pipe cutting machine. This kept the air clean without oil mist leaking outside. In addition, the cleaning time was reduced by adjusting the discharge port of the MISTRESA to blow off the oil on the pipe.
Metal press work
- Installation for preventing mist dispersion
- Mist collection
- Why we were consulted
- The mist was being sprayed, but since there was no cover, the sprayed mist was dispersing into the surrounding area. Visual inspection was required, and a transparent, easily adjustable cover was necessary.
- Before
- After
- Equipment installed
-
- CRM-H07-S23×1unit
- Side panels: Polypropylene
- Front panel: Curtain rail
- Installation work
- Electrical work
- Improvements
- The chemical substances to be sprayed were selected while paying attention to the material of the transparent cover in order to ensure a specific focus. A curtain-type design was chosen for easy full opening and closing.
Construction equipment manufacturing
- Mist collection from centerless grinding machine without cover
- Mist collection
- Why we were consulted
- Parts were being machined using a centerless grinding machine without a cover, but the generated oil mist making the area around the machine and the air dirty which was a problem.
- Before
- After
- Equipment installed
-
- CRM-H04 × 3 units
- Improvements
- The environment of the workplace was cleaned up by attaching an enclosure hood and a sheet to the source of the oil mist and collecting the oil mist with the mist collectors. The cost of the environmental improvement was significantly reduced with the SDG installation idea.
Metal Parts Manufacturing Industry
- Cleaning of the blower impeller
- Maintenance
- Why we were consulted
- The manufacturer had a blower made by an unspecified manufacturer that produced abnormal vibration, and they were troubled by uncertainty over what measures to take.
- Before
- After
- Equipment installed
-
- Cleaning of the impeller on the blower manufactured by another company as well as balance adjustments
- Improvements
- Performing impeller cleaning and balance adjustments eliminated the abnormal vibration and enabled normal blower operation.
Metal Parts Manufacturing Industry
- Collection of dust generated by the Burring machine
- Maintenance
- Why we were consulted
- Changing filters for dustresa and cleaning inside the machine.
- Before
- After
- Equipment installed
-
- Filter for CF-3700H
- Improvements
- By changing the filter and cleaning inside the machine /Dustresa, the intake capacity has been improved.
Heavy duty vehicles repairs industry
- Other companies' blower maintenance
- Maintenance
- Why we were consulted
- The customer using other company's blower for the paint booth for several years, the impeller was very dirty and the V-belt was stretched. This caused the blower performance was deteriorating.
- Before
- After
- Equipment installed
-
- Replacement blower belt
- Improvements
- The blower belt was replaced and the impeller was cleaned on site. Furthermore, impeller balancing was performed and the blower performance was restored.
Parts manufacturing
- Maintenance of V-belt driven blowers & Seminar
- Maintenance
- Why we were consulted
- The blower for the production line had been in use for many years and was starting to make strange noises. The customer was unable to detect normal sounds or the beginning of abnormalities, so the broken part became larger.
- Before
- After
- Equipment installed
-
- Replacement parts (8 types)
- Seminar was held to experience abnormal and normal sound before and after replacement of parts.
- Improvements
- Maintenance of the blower was requested to identify the cause and solution. The cause was a delay in finding an abnormality due to a lack of inspection. The seminar allowed the customer to experience the normality ⁄ abnormality of the blower and to inspect the unit themselves.
Automobile Parts Manufacture
- Modification of the duct inspection opening
- Other
- Why we were consulted
- Inspection and cleaning of the duct via the inspection opening was required frequently, and it was a nuisance having to remove the nuts and bolts each time.
- Before
- After
- Equipment installed
-
- The inspection opening was modified to enable interior inspections without tools.
- Improvements
- Modifying the inspection opening so that it could be opened and closed by handle, and without tools, enabled large reductions in manhours.
Sugar manufacture
- Insect control measures in the shipping process using conveyors
- Other
- Why we were consulted
- Insects invaded when unloading sugar from the second floor to the first-floor shipping area using a conveyor.
- Before
- After
- Equipment installed
-
- Cross-flow blower AC-154AMTD x 2 units
- Blower stand
- Insect net
- Improvements
- We were able to prevent insects from entering by installing a cross-flow fan and using an air curtain, which can avoid interfering with the operation of the conveyor. An insect net is installed to prevent insects from entering through gaps.
Medical instrument precision processing industry
- Improvement of air conditioning in the factory
- Other
- Why we were consulted
- Since the cold air from the air conditioner did not reach the entire factory, we were considering whether to add an air conditioner to circulate the air throughout the factory.
- Before
- After
- Equipment installed
-
- WR-200K 4 units
- Improvements
- By installing Windracers in front of the air conditioner, cold air reaches far, and no additional air conditioner is required.
Resin parts manufacturing plant
- Circulates air-conditioned cool air in the factory
- Other
- Why we were consulted
- The heat was generated from the injection molding machine that molds the resin parts, making the area around aisles unusually hot and this cause the air conditioning system did not working properly.
- Before
- After
- Equipment installed
-
- WR-200Wx11units
- Improvements
- The hot air was circulated by the windracer and the work environment was improved.
Chemicals manufacturing plant
- Blowing off rubbish from mold release agents booth
- Other
- Why we were consulted
- In the production line of automobile interior materials (polyurethane), reduce the defect rate by blowing away polyurethane waste with an air blower (compressor) before applying the mould release agents.
- Before
- After
- Equipment installed
-
- MDF-KSB-2200B-R213x2 units
- Control panels (inverter panels)
- Improvements
- Energy savings due to the switch from high output compressors to small output air blowers, and this also help the customer cost savings.
Auto parts manufacturing
- Improved ceiling area temperatures
- Other
- Why we were consulted
- The temperature in the ceiling area was very high because the heat from the carburizing furnace could not be ventilated properly and was trapped in the ceiling.
- Before
- After
- Equipment installed
-
- WR-200W-B0J1x2units (220V~240V 50Hz)
- Improvements
- Discharged the heat towards the opposite side of the windows by windracer and successfully reduce the temperature of the ceiling are by 5℃.
(From 48.5℃ to 43.5℃)
Event venue rental
- Mist generation in multi-purpose warehouses used for various events and other purposes to prevent heat build-up.
- Other
- Why we were consulted
- When using the multi-purpose warehouse for exhibition events in the summer, the warehouse was very hot and problematic because it was large and had no air-conditioning. The heat was not resolved by using ordinary circulators.
- Before
- After
- Equipment installed
-
- Windracer
- WR-200N x 6 units
- Improvements
- An SDG circulator called the "Windracer" was installed on a pillar at the venue, with an ingenious mounting seat that could change direction. In addition, a hose was attached to the outlet of the Windracer to generate mist, cooled by vaporisation heat, which cooled the venue as a whole.
Parts painting
- Replace from V-belt driven blower to direct-drive blower.
- Other
- Why we were consulted
- The blower on the production line had been in use for a long time and it was time to replace it with a new model as it could have affected the production line before it failed.
- Before
- After
- Equipment installed
-
- K1S5(DENCHOKU)
- Ductwork, hoods and construction.
- Improvements
- The SDG selected a new model and replaced the previous V-belt driven blower with a new direct-drive blower. The direct-drive system eliminated maintenance as there were no belts or other parts to inspect and replace. The existing pipework was also used to the maximum extent possible and construction costs and time could be minimised.
Automotive parts manufacturing
- Reducing the number of fans on the production line
- Other
- Why we were consulted
- Each production line had ten hanging fans, but their open motors let in dust and oily smoke, causing frequent breakdowns. A large blower was then installed, but it was bulky, noisy, and used a lot of electricity.
- Before
- After
- Equipment installed
-
- WR-200W-ST1-B0H1 x 16 units (4 units/1 production line)
- Instalation
- Improvements
- Four small "Windracer" blowers were installed on each line to reduce the total number of blowers. Their fully enclosed motors kept out dust, lowering the risk of breakdowns. This also improved energy efficiency and reduced noise.